Have you ever wondered if a bad valve cover gasket can cause the Check Engine Light? This article dives into the importance of the valve cover gasket in preventing oil leaks and engine damage. By understanding the symptoms, causes, and diagnosis of a faulty gasket, you can benefit from early detection and prevention of serious engine issues.
Learning about the role of a valve cover gasket and how it functions can help car owners identify potential problems before they escalate. By recognizing the signs of a failing gasket, such as oil leaks, burning smells, and misfires, individuals can take proactive steps to address the issue promptly. With insights into diagnosis methods and repair options, you can save time and money by maintaining their engine’s health and performance.
Key Points
- Valve cover gasket seals engine components
- Leaking oil, burning smell, misfires are symptoms
- Common causes: age, wear, installation errors
- Excessive vibration and engine overheating can lead to failure
- Bad gasket can cause check engine light indirectly
- Visual inspection, oil level check for diagnosis
- Compression test for thorough evaluation
- Repair involves removal, cleaning, and reinstallation
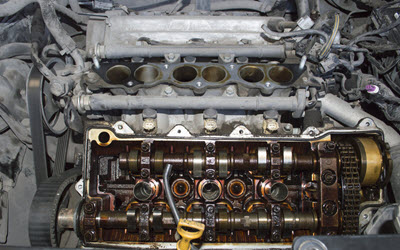
Just How a Valve Cover Gasket Functions
The valve cover gasket is an important component in your automobile’s engine. Situated in between the valve cover and the cyndrical tube head, its key feature is to produce a secure seal. This seal avoids oil from dripping out of the engine and pollutants from entering. The gasket likewise plays a crucial duty in preserving the pressure within the engine, which is needed for optimal efficiency.
The valve cover encloses the top of the engine, covering the valve train, that includes the camshafts, rocker arms, and valves. The gasket not just keeps the oil within the engine however additionally makes sure that the oil is effectively dispersed to the moving parts, reducing friction and wear. This is crucial for the engine’s long life and effectiveness.
Modern valve cover gaskets are commonly made from products like rubber, silicone, or cork, picked for their longevity and ability to withstand heats. Gradually, however, these materials can weaken because of consistent direct exposure to heat, stress, and engine fluids, resulting in gasket failure.
When the valve cover gasket falls short, it can lead to oil leakages, which might not just cause a mess yet likewise lead to substantial engine damage if not addressed promptly. Leaking oil can leak onto the exhaust manifolds, creating smoke and possibly also a fire risk. In addition, not enough oil levels can result in bad lubrication of engine parts, enhancing the danger of severe mechanical problems.
Comprehending exactly how a valve cover gasket functions is vital for diagnosing problems related to it. If you notice signs such as oil leakages, a burning oil scent, or engine misfires, it’s essential to inspect the valve cover gasket as a potential resource of the issue. Addressing gasket problems early can stop more serious and expensive engine damages.
Component | Feature |
Valve Cover Gasket | Develops a seal between the valve cover and cyndrical tube head, protecting against oil leakages and contaminants from entering. |
Valve Cover | Confines the top of the engine, covering the valve train components. |
Materials | Usually made from rubber, silicone, or cork for durability and warm resistance. |
In summary, the valve cover gasket is a small yet considerable component of the engine’s general capability. Its condition can straight influence the engine’s efficiency and health and wellness, emphasizing the value of routine upkeep and prompt repair work.
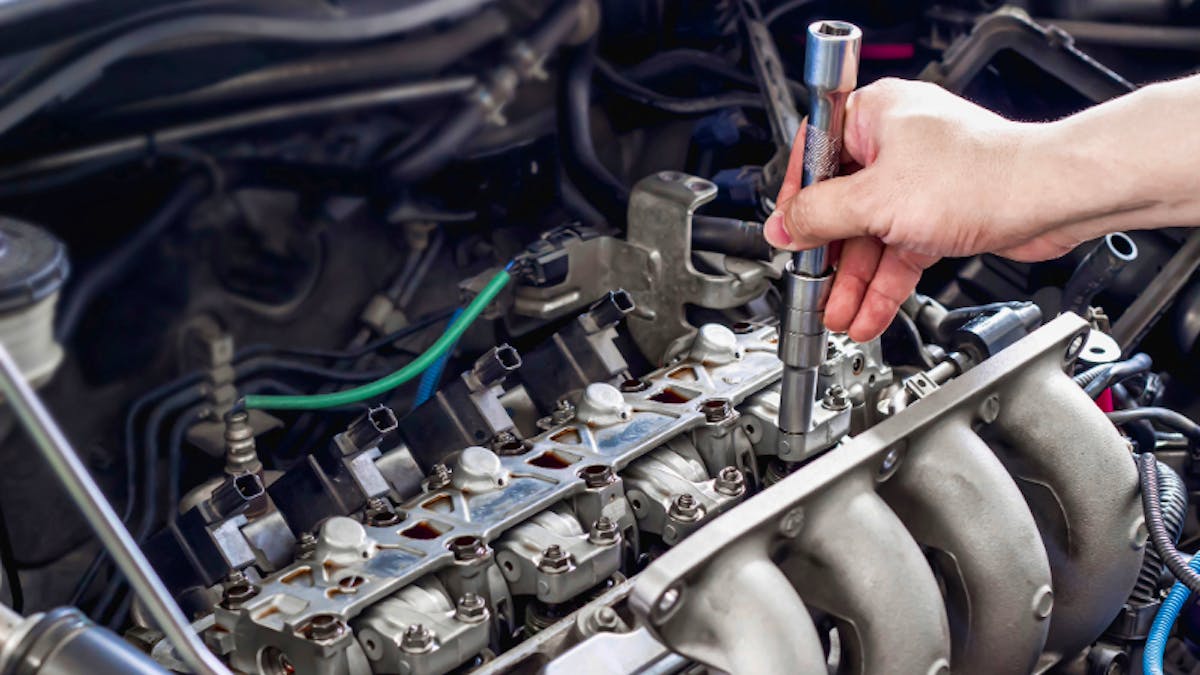
Symptoms of a Poor Valve Cover Gasket
A valve cover gasket is a vital part in your car’s engine, and recognizing the signs of a stopping working gasket can conserve you from much more extreme damage. Among the initial indications is oil leaks. When the gasket wears away, it can no more seal the valve cover properly, leading to oil leaking out. You might see oil spots under your vehicle or oil accumulating around the valve cover.
An additional symptom is the visibility of a burning oil smell. As oil leakages from the defective gasket, it can drip onto warm engine parts, creating a distinctive burning odor. This odor is usually much more visible when the engine is cozy or after driving for a while.
Additionally, a bad valve cover gasket can create the engine to run about or misfire. Oil that leakages from the gasket can pollute the ignition system, bring about inadequate ignition and performance concerns. This contamination can lead to a recognizable reduction in engine efficiency and an increase in gas consumption.
It’s also necessary to check for a check engine light. While a bad valve cover gasket might not straight cause the check engine light, the additional problems it causes, like misfires or oxygen sensor contamination, can. Modern automobiles are geared up with sensing units that discover these troubles, motivating the check engine light to brighten.
Noticeable signs on the engine itself can likewise suggest gasket failing. If you observe oil pooling around the valve cover or sludge accumulation, it’s a clear sign that the gasket is not executing its sealing feature effectively. These visual signs, combined with the other signs and symptoms, can assist in diagnosing a negative valve cover gasket.
Usual Root Causes Of Valve Cover Gasket Failing
A valve cover gasket plays an important duty in sealing the valve cover to the top of the engine cyndrical tube head, preventing oil leakages. However, a number of elements can result in its failing. Understanding these typical reasons can help in identifying and attending to problems quickly.
One of the primary root causes of valve cover gasket failing is age and wear. In time, the gasket product, typically made from rubber or cork, can deteriorate due to constant direct exposure to heats and engine oil. This destruction can cause the gasket to come to be brittle, fracture, or reduce, leading to oil leaks.
One more substantial factor is incorrect setup. If the valve cover gasket is not mounted properly or if the screws are not torqued to the manufacturer’s specs, it can cause an inappropriate seal. This can cause the gasket to fall short prematurely, causing oil leak and prospective engine problems.
Engine overheating is one more typical cause. Excessive warm can cause the gasket material to break down quicker. Overheating can occur as a result of different reasons, such as a malfunctioning air conditioning system, reduced coolant degrees, or a malfunctioning thermostat. When the engine runs hotter than typical, it increases the aging of the gasket.
The visibility of pollutants in the engine oil can additionally add to valve cover gasket failure. Dirt, debris, and sludge can accumulate and create the gasket to wear much faster. Routine oil adjustments and utilizing high-quality oil can assist mitigate this threat.
Furthermore, too much engine vibration can influence the honesty of the valve cover gasket. Resonances from the engine can create the gasket to shift or come to be misaligned, causing leaks. This is typically seen in engines with used or damaged electric motor places or in high-performance cars.
cause | Summary |
Age and Wear | Gasket material wears away gradually because of exposure to warmth and oil |
Incorrect Setup | Incorrect setup or inappropriate screw torque leads to an incorrect seal |
Engine Getting too hot | Too much warmth breaks down gasket product faster |
Contaminants in Oil | Dirt, particles, and sludge cause faster wear of the gasket |
Extreme Engine Vibration | Vibrations cause the gasket to shift or misalign, resulting in leaks |
Can a Poor Valve Cover Gasket cause the Inspect Engine Light?
One common question that develops when dealing with engine issues is whether a negative valve cover gasket can cause the Inspect Engine Light. The valve cover gasket plays an important role in sealing the valve cover to the top of the engine cyndrical tube head. This seal protects against oil from dripping out and contaminating various other engine parts. When the gasket stops working, oil leak is inescapable, which can lead to numerous engine issues.
A falling short valve cover gasket can indeed contribute to the activation of the Examine Engine Light. This generally occurs because the oil leakage causeed by the poor gasket can lead to secondary problems that the lorry’s onboard diagnostics system finds. For instance, oil leaking onto the engine’s ignition system or ignition coils can cause misfires. Engine misfires are an usual reason for the Check Engine Light to light up, as they influence the engine’s efficiency and exhausts.
Additionally, if the leaking oil makes its means to the oxygen sensing units or the catalytic converter, it can cause sensor malfunctions or damages to these essential components. Oxygen sensors are important for keeping track of the engine’s air-fuel mix, and any type of disturbance in their feature can prompt the Check Engine Light to come on. Similarly, oil contamination in the catalytic converter can bring about lowered efficiency or failure, which the vehicle’s diagnostics system will certainly flag.
In summary, while a negative valve cover gasket itself does not directly activate the Check Engine Light, the consequences of the oil leak it causes can cause conditions that do. It is important to resolve a defective valve cover gasket quickly to stay clear of more complications that may lead to an extra extreme and pricey repair service.
Detecting a Faulty Valve Cover Gasket
Diagnosing a defective valve cover gasket requires an organized approach to ensure precise recognition and ideal resolution. The primary step in this procedure is to carry out a visual inspection of the valve cover area. Try to find indications of oil leak around the edges of the valve cover gasket. This leakage typically materializes as oil spots or dampness on the engine block and other close-by components.
One more essential analysis action is to inspect the oil degree and condition. A relentless decrease in oil levels without any evident outside leakages could show that the oil is dripping inside as a result of a malfunctioning valve cover gasket. Furthermore, examine the oil for indicators of contamination, such as a milklike look, which suggests that coolant may be blending with the oil as a result of gasket failure.
One of the most telling signs of a negative valve cover gasket is the presence of oil in the spark plug wells. To inspect this, eliminate the stimulate plug cables or ignition coils and check the wells for oil. If oil exists, it is a strong indicator that the gasket has failed, permitting oil to leak into areas where it need to not be.
To even more validate the medical diagnosis, make use of a analysis scan device to examine for problem codes connected to the engine’s performance. While a negative valve cover gasket itself might not straight activate the check engine light, additional concerns caused by the oil leakage, such as misfires or sensing unit breakdowns, can. The check device can assist determine these associated concerns, providing a much more thorough understanding of the trouble.
For a more thorough analysis, think about conducting a compression examination. This examination aids establish the wellness of the engine’s cyndrical tubes and can reveal if the gasket failing has actually led to more considerable inner engine problems. Low compression in several cylinders may indicate that the valve cover gasket failure has actually impacted the cylinder head or valves.
Analysis Action | Summary | Indicators |
Aesthetic Assessment | Examine valve cover location for oil leaks | Oil spots, dampness on engine block |
Oil Degree Check | Inspect and keep track of oil levels | Persistent decline in oil levels |
Ignition System Well Assessment | Eliminate ignition system cables and check wells | Visibility of oil in cause plug wells |
Analysis Check | Use check tool to look for difficulty codes | Codes associated with misfires or sensor problems |
Compression Test | Test engine cyndrical tube compression | Low compression in cyndrical tubes |
By following these diagnostic steps, you can effectively determine a faulty valve cover gasket and understand the degree of the issue. Each action provides essential info that adds to a detailed diagnosis, guaranteeing that the underlying issue is properly attended to.
Fixing and Substitute Options for a Negative Valve Cover Gasket
Addressing a negative valve cover gasket is crucial to keeping your engine’s wellness and stopping additional difficulties. When it comes to fixing or changing a damaged valve cover gasket, there are a number of actions and factors to consider to ensure the process is effective and effective.
Evaluation and Preparation
Prior to beginning any type of repair work or substitute, it is essential to perform a comprehensive assessment. Look for indications of oil leakages around the valve cover area, and examine for any damages to the gasket itself. Gathering the essential tools and components, such as a brand-new gasket, gasket sealer, and ideal wrenches, is important to facilitate a smooth repair process.
Elimination of the Old Gasket
The initial action in the actual repair work is to get rid of the valve cover. This commonly includes loosening the screws that safeguard the cover in location. Meticulously raise the cover off to prevent damaging any type of parts. When the cover is removed, the old gasket can be taken off. Ensure all residues of the old gasket and any type of sealant are completely cleaned up from the valve cover and the engine surface.
Installation of the New Gasket
With the surface areas prepared, you can mount the brand-new gasket. If recommended for your certain car, use a slim layer of gasket sealer to ensure a correct seal. Location the new gasket onto the valve cover, guaranteeing it is correctly lined up. Meticulously position the valve cover back onto the engine, seeing to it the gasket remains in place.
Reassembly and Last Checks
When the new gasket remains in place, reattach the vavle cover by screwing the screws back in. It is essential to tighten the screws in a details sequence, generally beginning from the center and functioning outward, to prevent unequal stress on the gasket. After safeguarding the vavle cover, check for any type of signs of oil leakage around the new gasket. Begin the engine and monitor for any type of unusual audios or leaks.
Action | Activity |
Examination and Preparation | Check for oil leaks and collect required tools and parts. |
Removal of the Old Gasket | Remove the valve cover and old gasket, clean surface areas. |
Installation of the New Gasket | Apply gasket sealer if required, put new gasket, placement valve cover. |
Reassembly and Last Checks | Tighten up screws in turn, check for leaks, begin the engine. |
By complying with these steps, you can properly change a negative valve cover gasket and potentially deal with any concerns associated with the check engine light. Normal upkeep and prompt attention to any kind of indicators of gasket failure will assist ensure your engine runs smoothly and efficiently.
Can a Bad Valve Cover Gasket Cause Check Engine Light?
One common question that arises when dealing with engine issues is whether a bad valve cover gasket can cause the Check Engine Light. The valve cover gasket plays a crucial role in sealing the valve cover to the top of the engine cylinder head. This seal prevents oil from leaking out and contaminating other engine components. When the gasket fails, oil leakage is inevitable, which can lead to various engine problems.
A failing valve cover gasket can indeed contribute to the activation of the Check Engine Light. This typically happens because the oil leak caused by the bad gasket can lead to secondary issues that the vehicle’s onboard diagnostics system detects. For instance, oil leaking onto the engine’s spark plugs or ignition coils can cause misfires. Engine misfires are a common reason for the Check Engine Light to illuminate, as they affect the engine’s performance and emissions.
Moreover, if the leaking oil makes its way to the oxygen sensors or the catalytic converter, it can cause sensor malfunctions or damage to these critical components. Oxygen sensors are vital for monitoring the engine’s air-fuel mixture, and any disruption in their function can prompt the Check Engine Light to come on. Similarly, oil contamination in the catalytic converter can lead to reduced efficiency or failure, which the vehicle’s diagnostics system will flag.
In summary, while a bad valve cover gasket itself does not directly cause the Check Engine Light, the consequences of the oil leakage it causes can lead to conditions that do. It is essential to address a faulty valve cover gasket promptly to avoid further complications that might result in a more severe and costly repair.