Ball valves are indispensable components in fluid systems, controlling the flow of liquids and gases with a rotating ball. Their versatility and reliability have made them ubiquitous in various industries, including oil and gas, chemical processing, and water distribution. Understanding ball valve sizes is crucial for ensuring proper system operation and preventing costly failures. This comprehensive guide delves into the intricacies of ball valve sizes, exploring international standards, nominal pipe sizes, flow rates, and critical factors for selecting the appropriate size. Additionally, a detailed table is provided for quick reference and comparison of ball valve sizes.
International Standards
To ensure global compatibility and adherence to quality and safety standards, ball valve sizes are defined by several international organizations. These standards provide guidelines for dimensions, materials, testing, and performance requirements, ensuring consistency and reliability across manufacturers.
- ISO/IEC: International Organization for Standardization/International Electromechanical Commission
- API: American Petroleum Institute
- AWWA: American Water Works Association
- ASME: American Society of Mechanical Engineers
Nominal Pipe Size (NPS)
Nominal Pipe Size (NPS) is a standardized measurement system used to identify the approximate diameter of pipes and fittings. It is important to note that NPS does not always correspond directly to the actual inner diameter of the pipe. For ball valves, NPS typically refers to the size of the pipe end connection.
Common NPS Values for Ball Valves:
- 1/4″
- 1/2″
- 3/4″
- 1″
- 1-1/4″
- 1-1/2″
- 2″
- 2-1/2″
- 3″
- 4″
- 6″
- 8″
- 10″
- 12″
- 14″
- 16″
- 18″
- 20″
Actual Flow Rates
The flow rate through a ball valve is influenced by several factors, including the valve size, ball type, and fluid properties. Understanding these factors is crucial for selecting a valve that meets the required flow rate for the specific application.
- Valve Size: Larger valves generally have higher flow capacities compared to smaller valves.
- Ball Type: Full-port ball valves, which have a ball with a bore that extends through the entire diameter of the valve, offer higher flow rates than reduced-port ball valves.
- Flow Coefficient (Cv): This dimensionless parameter represents the flow rate of water through a valve at a pressure drop of 1 psi. It is a useful metric for comparing the flow capacity of different valves.
- Fluid Properties: The density and viscosity of the fluid being controlled also impact the flow rate.
Calculating Flow Rate:
The flow rate (Q) through a ball valve can be estimated using the following formula:
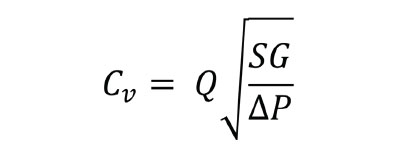
where:
- Q = Flow rate (gallons per minute)
- Cv = Flow coefficient
- ΔP = Pressure drop across the valve (psi)
- SG = Specific gravity of the fluid
Selecting the Right Size
Choosing the appropriate ball valve size is critical for optimal system performance and efficiency. Several factors need to be considered during the selection process:
- Pipe Size: The NPS of the ball valve should match the inner diameter of the pipe it is connecting to.
- Flow Rate: Determine the required flow rate and select a valve with a sufficient Cv to meet the demand.
- Pressure Drop: Consider the acceptable pressure drop across the valve and ensure it is compatible with the system requirements.
- Materials: The materials used in the construction of the valve should be compatible with the fluid being handled and the operating environment.
Additional Considerations:
Beyond the factors mentioned above, other considerations may influence ball valve size selection:
- Valve Type: Different types of ball valves, such as floating or trunnion-mounted, may have specific size limitations.
- Space constraints: The available space for valve installation may limit the maximum allowable size.
- Cost: Larger valves generally have higher costs associated with them.
- Maintenance: Accessibility and ease of maintenance should be considered during size selection.
Ball Valve Size Table
The following table provides a comprehensive overview of ball valve sizes, including NPS, approximate dimensions, and flow coefficients for various valve types:
NPS |
Approximate Dimensions (in inches) |
Flow Coefficient (Cv) |
1/4 |
0.5 x 1.5 |
5 |
1/2 |
0.75 x 2.25 |
10 |
3/4 |
1 x 2.75 |
15 |
1 |
1.25 x 3.25 |
20 |
1-1/4 |
1.5 x 4 |
25 |
1-1/2 |
1.75 x 4.5 |
30 |
2 |
2.25 x 5.25 |
40 |
2-1/2 |
2.75 x 6 |
50 |
3 |
3.25 x 7 |
60 |
4 |
4.25 x 8.5 |
80 |
6 |
6 x 11 |
120 |
8 |
8 x 14 |
160 |
10 |
10 x 17 |
200 |
12 |
12 x 20 |
250 |
14 |
14 x 23 |
300 |
16 |
16 x 26 |
350 |
18 |
18 x 29 |
400 |
20 |
20 x 32 |
450 |
Conclusion
Understanding ball valve sizes is essential for engineers, designers, and technicians working with fluid systems. By adhering to international standards, considering nominal pipe sizes, calculating flow rates, and carefully evaluating selection factors, it is possible to choose the optimal ball valve size for each application. This comprehensive guide, along with the provided table, serves as a valuable resource for navigating the complexities of ball valve sizing, ensuring efficient and reliable system operation.
Lixin Valve is a Professional Industrial Ball Valve Manufacturer, Please feel free to contact!